Ride the FUTURE
WITH — ARSTECH
Ride the FUTURE
WITH — ARSTECH
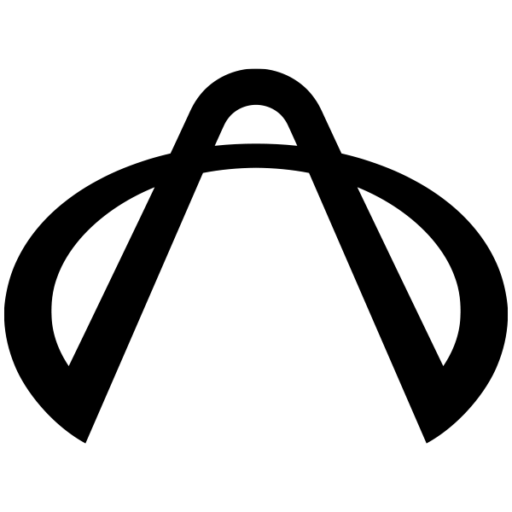
ARS TECH — ART
and TECHNOLOGY
in one Company
ARS stands for Advances Reinforced Structures, but the name incorporates a rich range of Latin meanings such as art, skill, technique, craftsmanship, and science, highlighting the fusion of traditional craftsmanship and advanced process technologies. ARS TECH’s vision is to introduce a new paradigm that pushes composite production to the next level in the automotive industry.
ARS TECH embraces this industrial calling by developing and manufacturing carbon fiber chassis and body components, exclusively dedicated to the Automotive-Motorsport sector, where performance matters.
ARS TECH embraces this industrial calling by developing and manufacturing carbon fiber chassis and body components, exclusively dedicated to the Automotive-Motorsport sector, where performance matters.
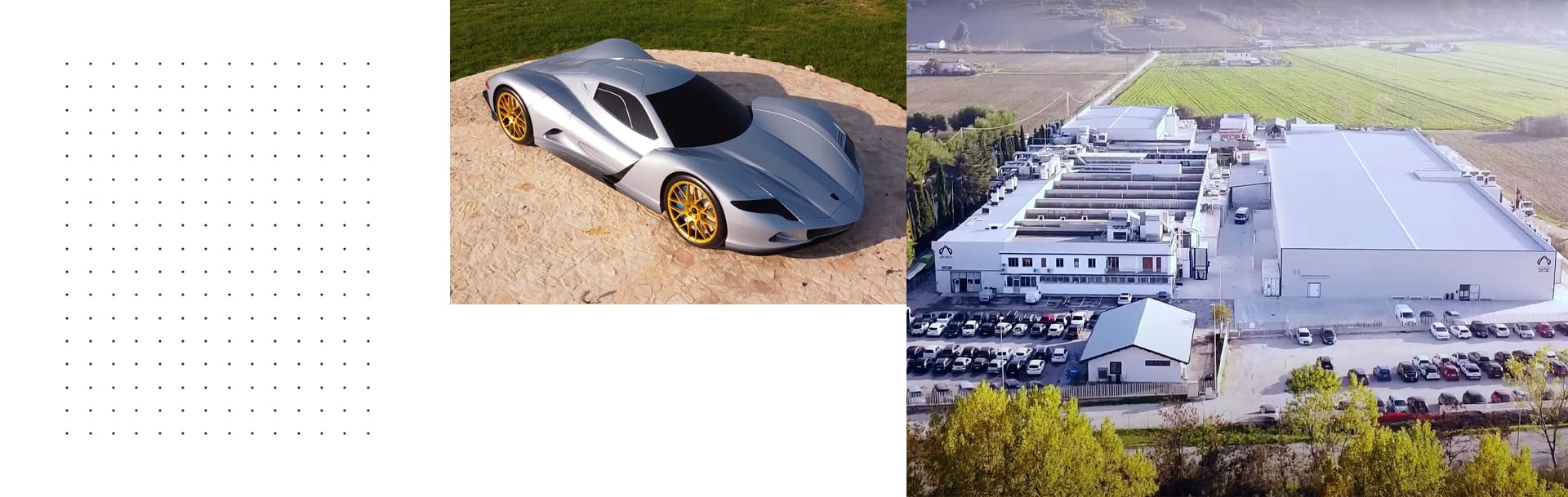
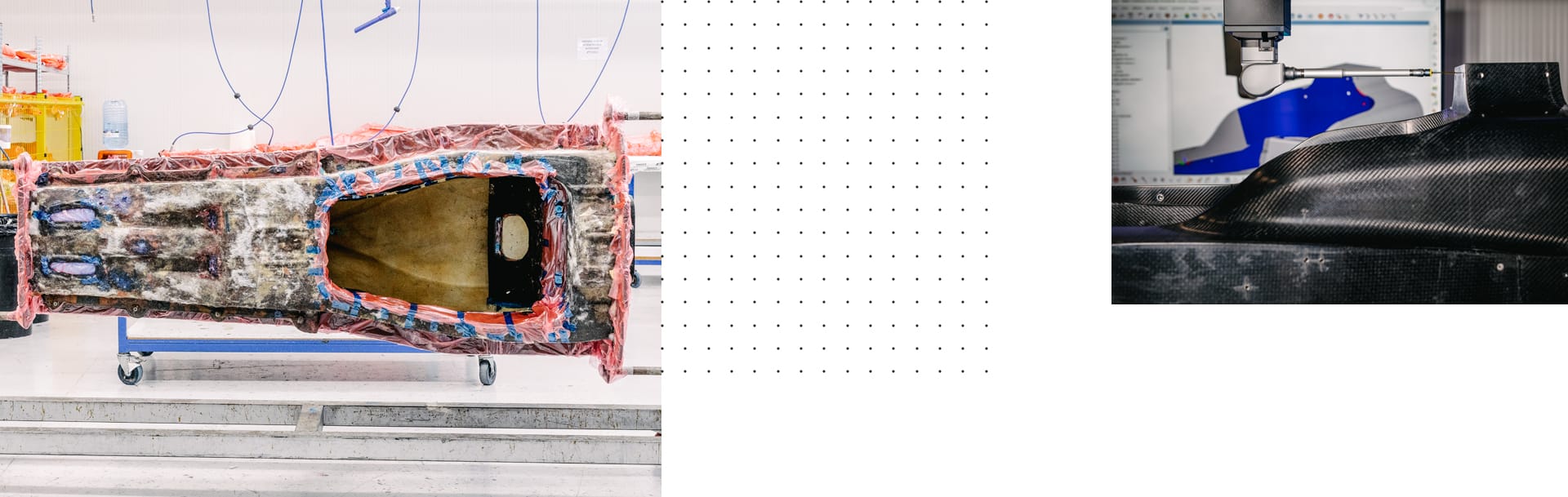
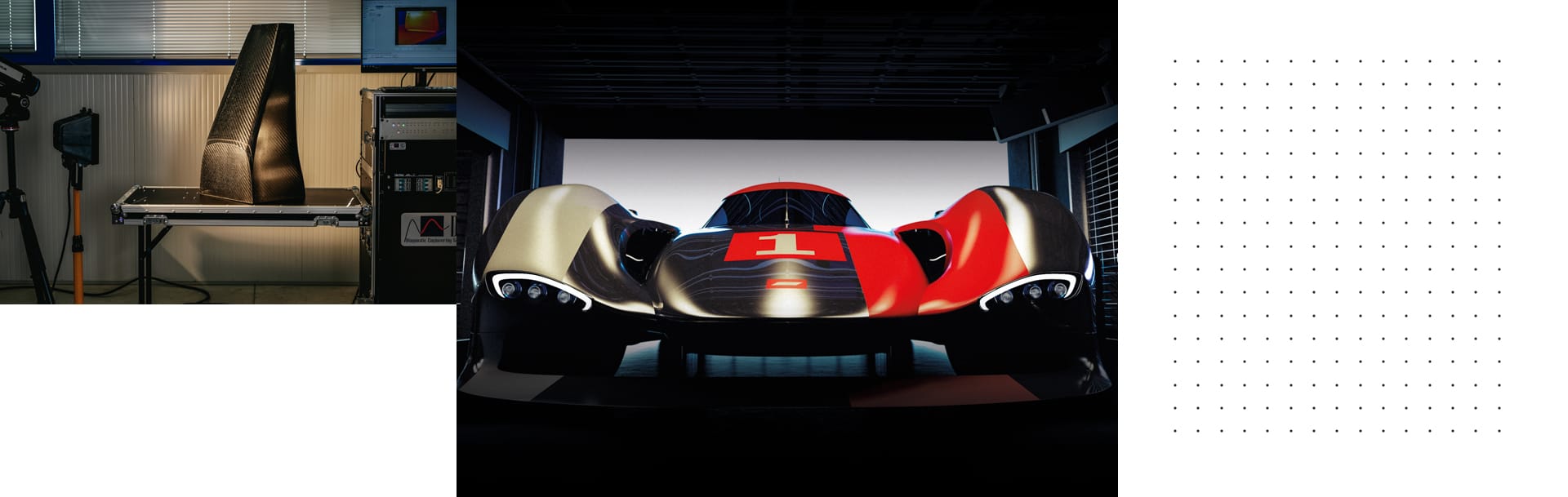
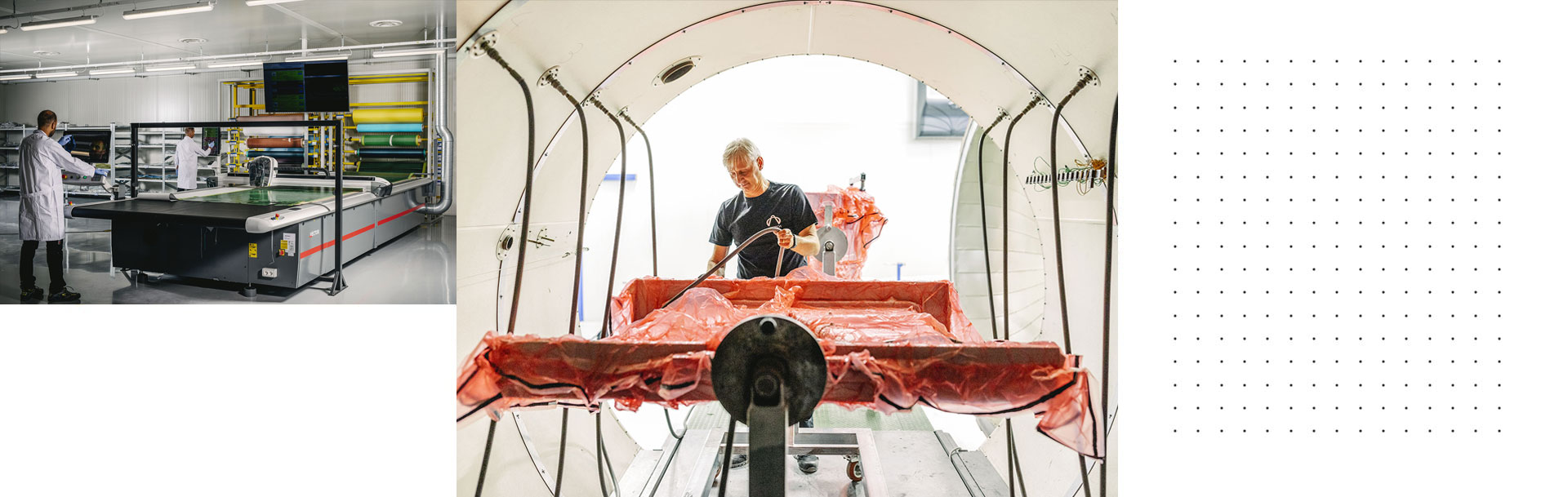

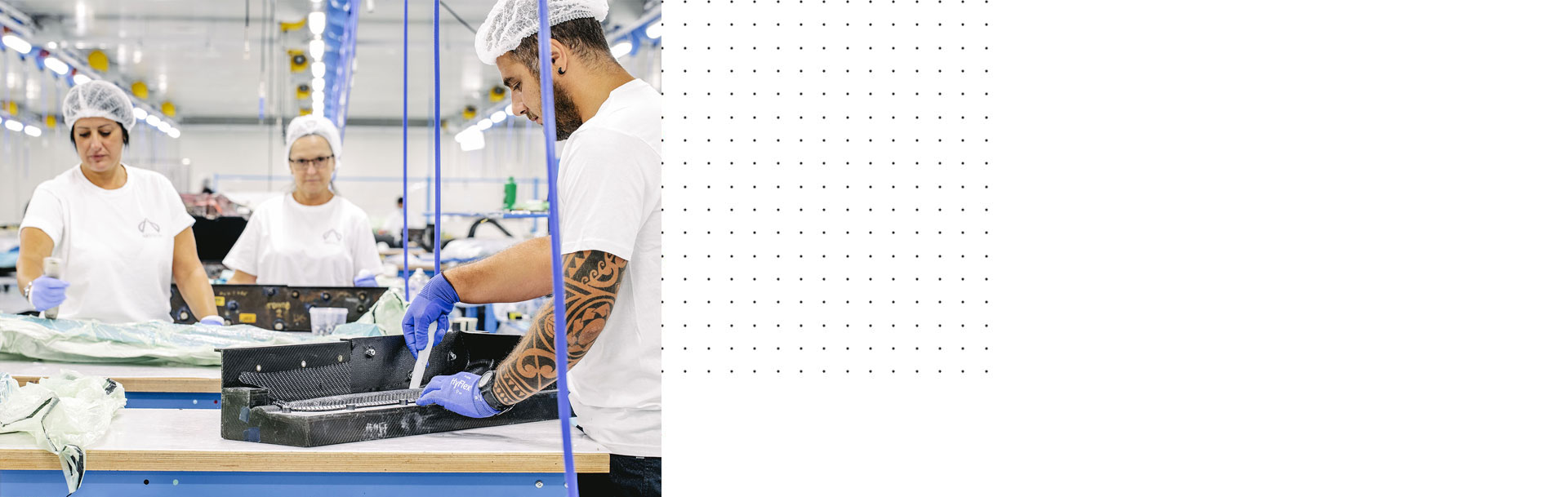
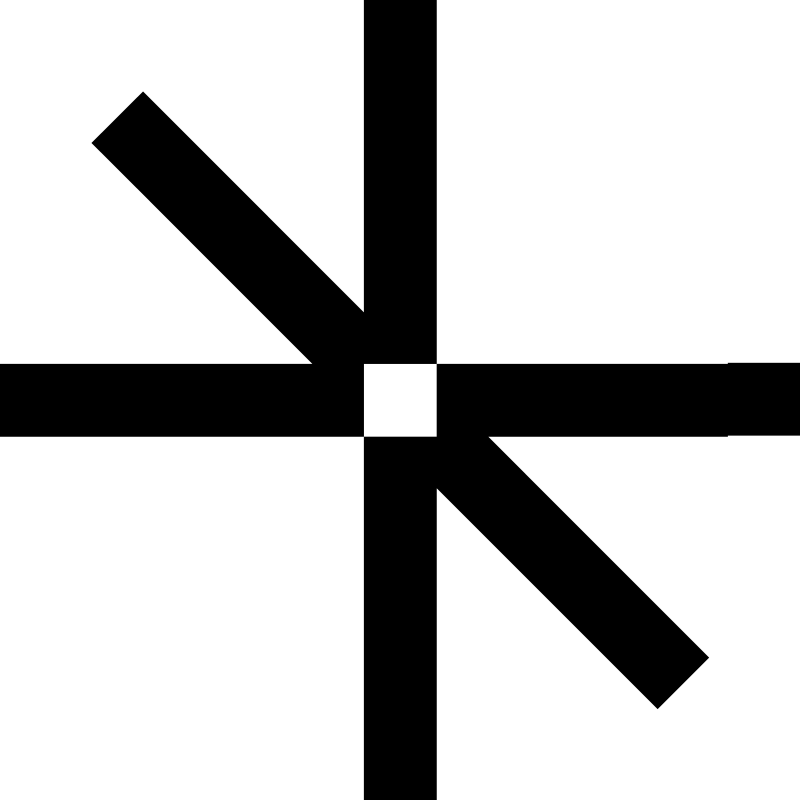
Passion for —
HIGH PERFORMANCE
The history of a
long-standing territory
and know-how
ARS TECH traces its roots to the extensive experience of professionals who have played a significant role in the history of composite materials.
Continuously looking to the future, ARS TECH leverages the knowledge acquired over the years to create a cutting-edge production hub consisting of four interconnected facilities and dedicated departments for engineering, R&D, and materials.
Continuously looking to the future, ARS TECH leverages the knowledge acquired over the years to create a cutting-edge production hub consisting of four interconnected facilities and dedicated departments for engineering, R&D, and materials.
Despite its international orientation, as evidenced by collaborations with automotive companies worldwide, ARS TECH maintains a strong connection with its local community, a foundational value of its history. A concrete example of this commitment to the local community is a significant project funded in 2021: the redevelopment of the Controguerra roundabout, inside it, a 1:1 scale replica of the Aspark Owl, a hypercar whose components were entirely produced by ARS TECH, has been placed. This initiative demonstrates the company’s interest in the growth and enhancement of the territory in which it operates.
2014
—
Start of collaboration with Tatuus Racing S.p.a. and Japanese automaker Dome Co.
2015
—
Commencement of collaboration with French racing team ORECA.
2016
—
Development of the Norma M30 LMP3 and the beginning of collaboration with the automaker Duqueine.
2017
—
Collaboration with the German automaker Apollo Automobil for the creation of the APOLLO Intensa Emozione.
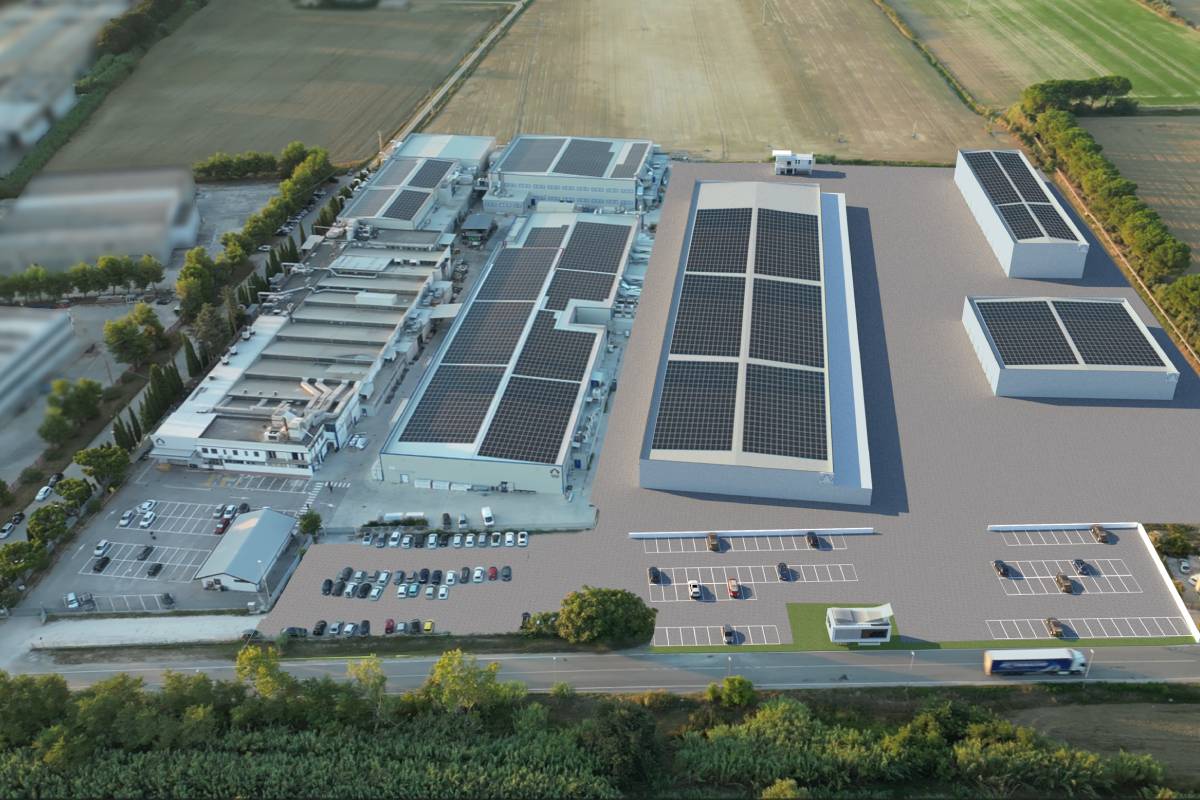
2018
—
Production of the LMP1 Ginetta, a racing car produced by the eponymous British company.
2019
—
Development of the Ginetta LMP3. Collaboration with the Turin-based automaker Manifattura Automobile Torino (MAT) for the creation of the high-speed and powerful Japanese hypercar Aspark Owl.
2020
—
Collaboration with the French manufacturer Mygale for the production of the FORMULA 4 GEN 2.
2022
—
New collaboration with TATUUS for the FORMULA 4 GEN 2 and with the automotive company Isotta Fraschini for the creation of the Tipo 6 LMH.
ARS TECH is constantly committed to pushing its boundaries, continuously devising new, efficient, and environmentally sustainable production processes. This approach is bolstered by research and development programs, the implementation of technological innovations, and plans for expanding production capacity.
Industrial programs focused on environmental sustainability and workforce growth are tangible evidence of ARS TECH’s unwavering dedication to achieving these goals.
Industrial programs focused on environmental sustainability and workforce growth are tangible evidence of ARS TECH’s unwavering dedication to achieving these goals.
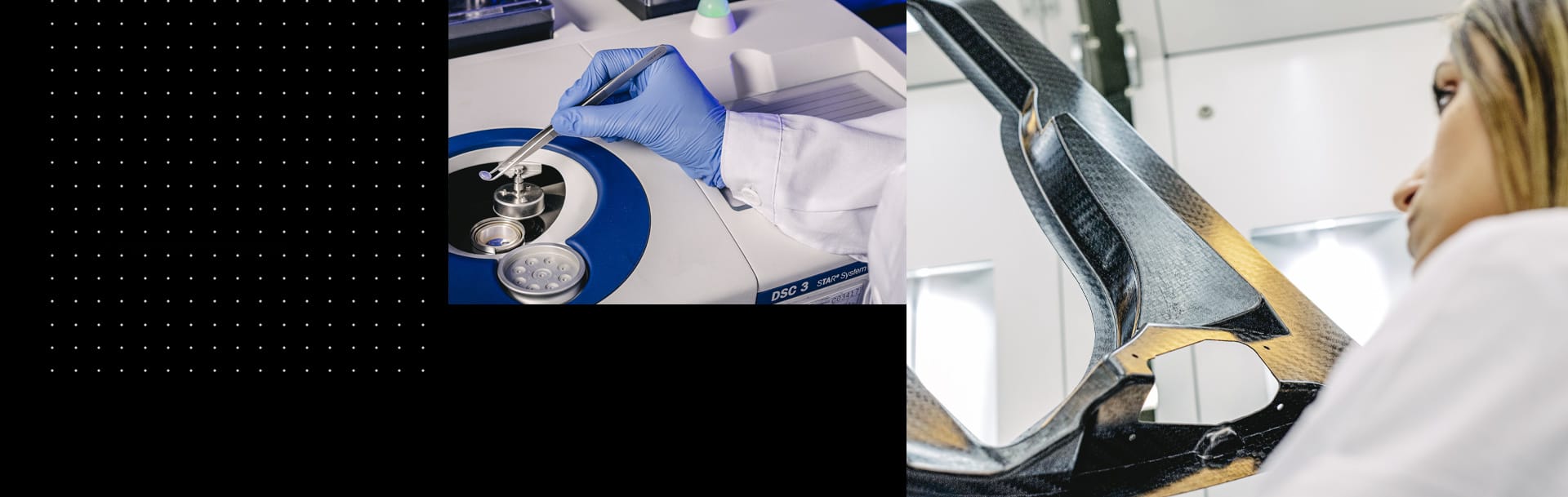
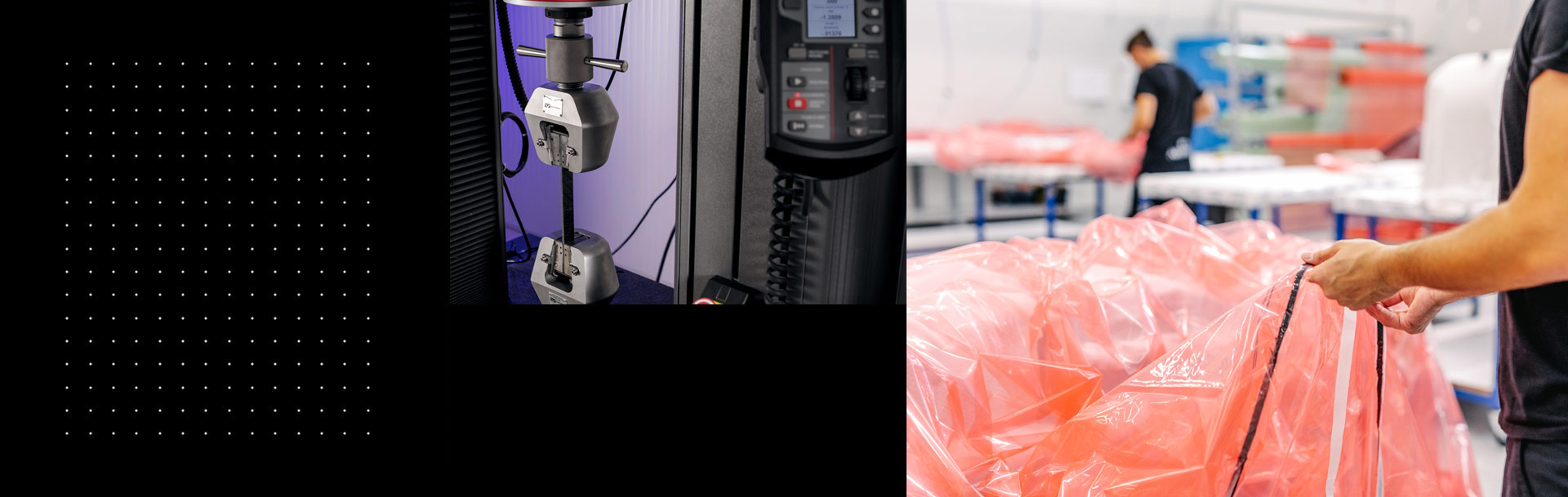
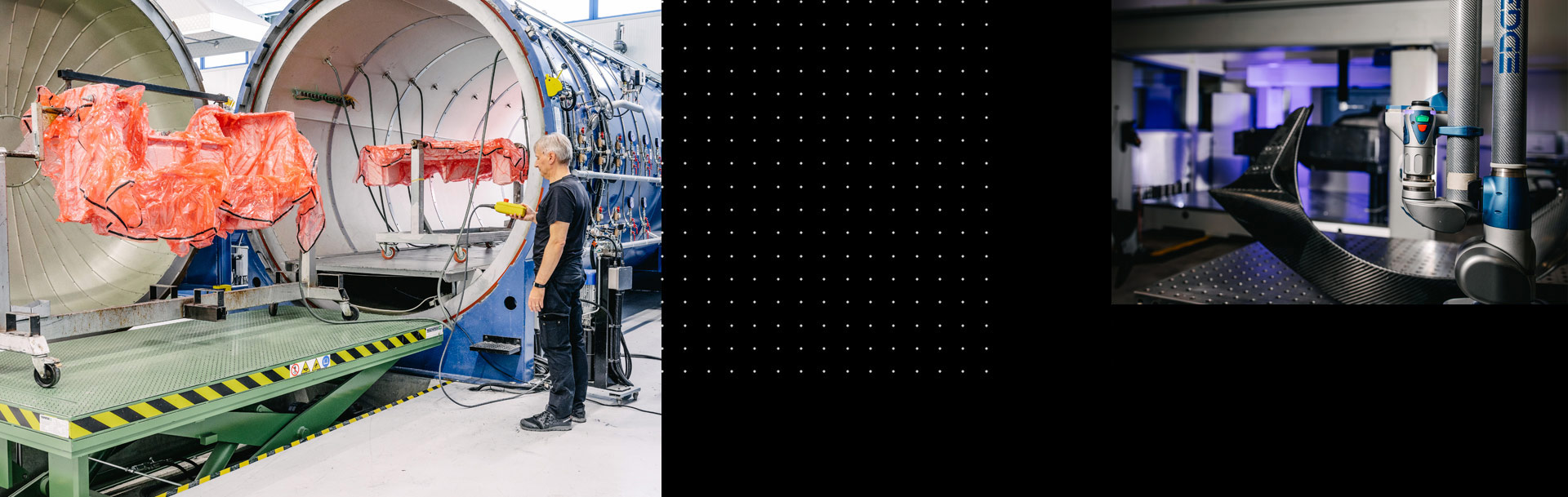
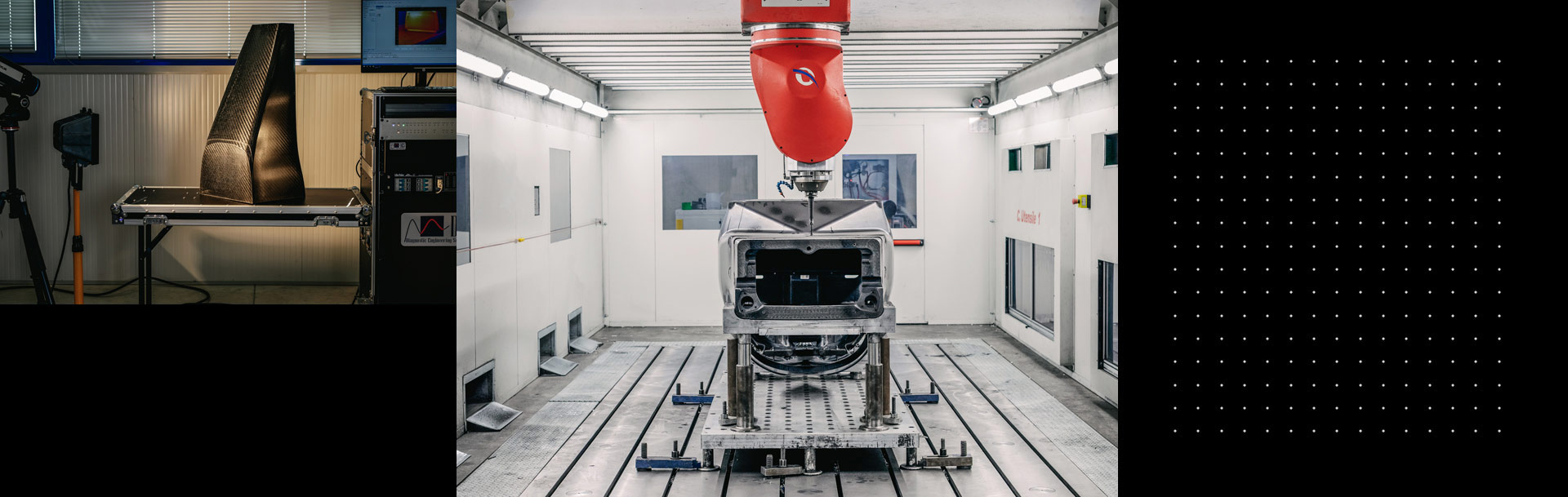
35.000.000 €
Turnover
28.000
Components produced
24.000 mq
Of surface of surface area
+ 500
Human resources employed
200
Racing Car Chassis Produced
35
Years of Experience in the Industry
10
Countries Served Worldwide
11
Autoclaves
4
Manufacturing Plants
ARS TECH has implemented a Quality Management System in accordance with the UNI EN ISO 9001:2015 standard. The project began in 2016, the year in which the company achieved ISO 9001 certification, thereby receiving official recognition of its corporate Quality Management System.
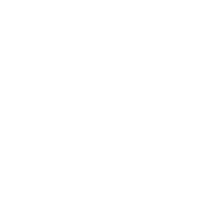
35.000.000 €
Turnover
28.000
Components produced
24.000 mq
Of surface of surface area
+ 500
Human resources employed
200
Racing Car Chassis Produced
35
Years of Experience in the Industry
10
Countries Served Worldwide
11
Autoclaves
4
Manufacturing Plants
Keep in —
TOUCH
Do you want to request more information?
We are ready to respond to your inquiries.
We are ready to respond to your inquiries.